Taiwanese Fruit Distributor Tracks Fresh Produce Via RFID
09 Oct 2013
By Claire Swedberg
Taiwanese fruit producer Je-Nong Cooperative Farm is employing an RFID-based solution to document the receipt and processing of its fresh fruit at its facility in Miaoli County. By using passive EPC ultrahigh-frequency (UHF) RFID tags integrated in plastic crates, the company can monitor every step that the fruit undergoes, as it happens, and the conditions within coolers before the fruit is transported to stores throughout Taiwan, as well as in China, Japan and Korea.
The system, developed by EPC Solutions Taiwan, consists of passive UHF tags, embedded in plastic crates, that are read at key locations during processing. The solution also includes active RFID sensor tags situated at cooling units to transmit temperature data to back-end software supplied by Taiwan Futaba Electronics.
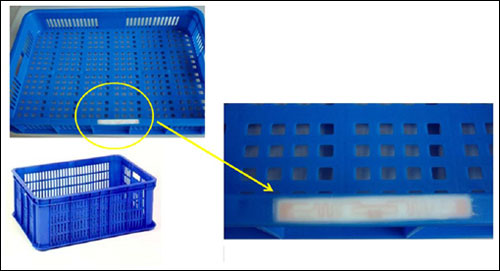
Je-Nong Cooperative Farm processes a total of 350,000 kilograms (386 tons) of grapes, pears, oranges, mangos and other fruit annually. After receiving the fruit from Taiwanese farms, the cooperative cleans, disinfects and waxes it—and, in some cases, color is applied. The produce must then sit in cold storage until being shipped to a store. The company faced a daunting task in monitoring the fruit from when it is picked until the completion of processes at its own site, as well as ensuring that the product leaves for the customer's site in optimal condition. Je-Nong previously employed a series of manual tracking methods that were time-consuming and resulted in the waste of packing material. With passive UHF RFID tags affixed to plastic reusable cartons, and with readers deployed at specific locations, the company now knows when harvesting occurs, as well as when every crate undergoes each process. The active 2.4 GHz tags transmit the temperature and humidity within each cooler in which the fruit is then stored.
Prior to the RFID solution's installation, farmers picked the fruit and loaded it into cardboard cartons that they then shipped to Je-Nong. The cooperative transferred the fruit from the boxes into plastic crates that can withstand cleaning, disinfection and waxing processes. This, the company reports, was not only time-consuming but also wasteful, since the cardboard containers could not be reused. Je-Nong's staff then manually measured and recorded the produce's weight.
Because farmers use chemical sprays to kill insects or other pests in the fields, the fruit must undergo rigorous cleaning in order to ensure that all traces of chemicals are removed from the product prior to packing. To that end, the fruit passes over rotary brushes on a conveyor, where it is scrubbed and rotated, and is then sent to a washing machine that sprays each piece with a cleaner from all sides.
The fruit next moves through a soaking tank filled with a solution of detergents and water softeners, in order to remove any dirt, bacteria or remaining insects. Wax is then applied to the fruit to protect it from scarring or moisture loss, which also extends the product's lifespan. Finally, the produce is placed into a cooler, the temperature and humidity of which was tracked using sensors that were manually monitored 24 hours a day, seven days a week, in order to maintain a record of those conditions, says Hsin-An Chang, Je-Nong's general manager. All of the recorded weight and sensor data can then be shared with customers; those in Japan have the most stringent requirements related to sensor-based data about the produce, Chang notes.
To reduce some of the labor costs expended on these processes, Je-Nong began working with Taiwan Futaba Electronics Co. and EPC Solutions Taiwan in 2011 to develop a solution that would include an RFID tag, integrated into a plastic crate, that could tolerate exposure to water and solvents, as well as the impact related to shipping, explains T.H. Liu, EPC Solutions Taiwan's president.
EPC Solutions Taiwan designed the CrateTag, made with an Alien Technology Higgs-3 chip and encapsulated with a polyethylene material. The CrateTag is able to survive temperatures of up to 240 degrees Celsius (464 degrees Fahrenheit), which can occur during the plastic-injection molding used to manufacture the crate. During this molding, Liu says, the encapsulated housing fuses with the crate's plastic material.
With the new system in place, a farmer anticipating a harvest sends Je-Nong a request for RFID-tagged plastic crates. The firm uses an Alien ALR-9650 RFID reader (which includes an integrated circularly polarized antenna) to input all crate ID numbers into its system and link those IDs to that specific farmer. The farm then fills the crates with fruit and ships them back to Je-Nong.
Je-Nong's facility consists of a 100,000-square-foot building housing eight cooling units for storing fruit. The cooperative has installed an Alien ALR-9900+ reader at each unit.
When the produce is weighed, the crate is placed onto a scale, where an ALR-9650 reader captures the crate's unique ID number. The system then links that ID and weight to data regarding the produce packed within, along with its farm of origin. Futaba software links that information with the weight captured by the scale. As the crate passes though the cleaning and disinfection stations, interrogators capture these events as well, creating a record indicating when each process was completed.
The crates are then transported to coolers, each with a single ALR-9900+ reader and four antennas installed at its doorway. Installed within each cooler is a Taiwan Futaba remote-controlled wireless temperature and humidity sensor. The battery-powered 2.4 GHz wireless sensor transmits data to a single reader installed in the cooler and cabled to the computer system on which the software resides. That software collects sensor data and issues an alert, via a text message, to management in the event that the conditions fall outside preset parameters. This allows the managers to quickly respond to temperature changes before the fruit can become damaged. Thesensor data is also linked to each crate's unique ID, thereby marrying the temperature and humidity data with the specific products.
When the produce stored in those cooling units is exported to Japan, Je-Nong provides Japanese quarantine officers with data about each crate of produce, in order to prove that the company has maintained the products' freshness. This information can also be shared with customers in Taiwan, China and Korea.
Since the solution's installation in early 2012, Chang reports, Je-Nong Cooperative Farm has attained a return on its investment, based on a reduction in labor costs. What's more, he says, the system provides a more reliable product for customers, since the company now has automated proof of the fruit's conditions while at the Je-Nong facility. "We are so happy to have this system," Chang states, "and happy to demo to other cooperative farm companies.